سازه فلزی یا اسکلت فولادی، مجموعهای منظم از تیرها و ستونهای فولادی است که به شکل عمودی و افقی و با استانداردهای دقیقی در کنار یکدیگر قرار گرفته و محکم به هم وصل شدهاند. دو روش کلی برای برپایی و اتصال اجزای سازه فولادی وجود دارد که عبارتند از استفاده از پیچ، مهره و یا جوشکاری.
امروزه اسکلت فلزی به دلیل سهولت برپایی، افزایش سرعت ساخت و ساز و البته مقاومت بالای خود در بسیاری از کشورها، اولین گزینه برای ساخت پروژههای بزرگ و ساختمانهای مرتفع محسوب میشود و جای سازههای بتنی را گرفته است.
فهرست مطالب
تاریخچه اسکلت فلزی
اسکلت فلزی از زمان رشد صنایع تولید فولاد در اوایل قرن بیستم، به تدریج در پروژههای ساختوساز به کار گرفته شد. در ادامه و با تسهیل فرآیند تولید آهن و مشتقات آن در دوران بعد از جنگ جهانی دوم، عموم ساختمانها در کشورهای پیشرفته با اسکلت فولادی ساخته شدند.
گرچه ابتدا از چدن در سازه فلزی استفاده میشد اما به تدریج آهن کم کربن و سپس انواع مقاطع فولادی در اشکال و آلیاژهای گوناگون به عنوان مصالح اصلی سازه فولادی مورد استفاده قرار گرفتند.
انواع سازه فولادی
اسکلت فولادی همانطور که گفتیم مجموعهای متشکل از تیرها و ستونهای فولادی است، اما از نظر روش اتصال، دو نوع متفاوت از سازه فلزی قابل اجراست که عبارتند از سازه فولادی پیچ و مهرهای و اسکلت فولادی جوشکاریشده. در ادامه به اختصار به توضیح هر مورد و تفاوتهای آنها میپردازیم.
اسکلت فولادی پیچ و مهره ای
ساخت اسکلت فلزی پیچ و مهره، مطمئنترین، مستحکمترین و البته سریعترین روش برپایی سازه فلزی است. در این شیوه، قطعات فولادی به طور کامل در کارخانه آماده شده و بعد از انتقال به محل پروژه، با پیچ و مهرههای مناسب و مخصوص به هم وصل میشوند.
از این شیوه معمولا در برپایی اسکلت برجها و آسمانخراشهای بزرگ استفاده میشود و عموما پروژههایی که نیاز به سرعت عمل در اجرا دارند با این شیوه اجرا میشوند.
با وجود مزایای این روش، توجه داشته باشید که اندازه و ابعاد دقیق قطعات فولادی در این شیوه بالاترین اهمیت را دارد و اگر مشکلی در اتصال یا برپایی سازه به دلیل نقص قطعات وجود داشته باشد، ناگزیر باید قطعه به کارخانه ارجاع داده شده و مجددا ساخته شود و این امر میتواند زمانبر باشد.

اسکلت فلزی جوشکاری شده
در شیوه اجرای اسکلت فلزی جوشی، قطعات و ستونهای فلزی با جوش به هم وصل میشوند. توجه داشته باشید که کیفیت جوشها برای دوام اسکلت در این شیوه اهمیت زیادی دارد و به همین دلیل باید تمام فرآیند جوشکاری توسط افراد متخصص و باتجربه انجام شود.
معمولا از شیوه جوشکاری در پروژههایی نسبتا کوچکتر با نقشه ساده و متراژ کمتر استفاده میشود چراکه اجرای شیوه جوشکاری در پروژههای بزرگ دشوار و زمان بر است.
مزایای سازه فولادی
از جمله مهمترین مزایای اسکلت فلزی باید به موارد زیر اشاره کرد:
- مقاومت و استحکام بالا: فولاد به طور طبیعی مقاومت بالایی دارد و در زمان ساخت قطعات فولادی، فرآیند تولید با سهولت بیشتری همراه است. این ویژگی در پروژههایی با ارتفاع بالا و روی زمینهای سست اهمیت زیادی دارد. در واقع، اسکلت فلزی میتواند کیفیت مناسب و سهولت اجرا را همزمان فراهم کند.
- مقاومت متعادل مصالح: فولاد مقاومت بالایی در برابر کشش و فشار دارد و در برش نیز عملکرد خوبی از خود نشان میدهد. این ویژگی باعث میشود که در تغییر بارها، نیروی فشاری و کششی به راحتی قابل تعویض باشد و مقاطع فولادی به خوبی واکنش نشان دهند.
- خواص ارتجاعی: فولاد به دلیل همگن بودن، خواص ارتجاعی دقیقی دارد که میتوان آن را به طور نسبی به راحتی محاسبه کرد. فولاد تا محدوده وسیعی از تنشها از قانون هوک پیروی میکند، که این امکان را میدهد که ممان اینرسی مقاطع فولادی با دقت در محاسبات وارد شود.
- شکلپذیری: فولاد دارای خواص شکلپذیری عالی است که اجازه میدهد نیروهای دینامیکی و ضربهای سنگین را تحمل کند، بدون اینکه به خرابی منجر شود. این ویژگی سبب میشود که فولاد عملکرد بهتری در برابر بارهای سنگین و نیروهای ضربهای داشته باشد.
- خواص یکنواخت: مقاطع فولادی معمولاً در کارخانهها و با استانداردهای دقیق تولید میشوند و خواص آنها در مقایسه با سایر مصالح بسیار یکنواخت است. این یکنواختی خواص باعث کاهش ضریب خطا و در نتیجه صرفهجویی در مصرف مصالح میشود.
- پیوستگی مصالح و دوام بالاتر: یکی از دلایل مقاومت بالای اسکلت فلزی، پیوستگی و همگنی مصالح آن است که سبب میشود اسکلت فلزی در برابر پدیدههایی مانند زمینلرزه مقاومت بالایی داشته باشد.
- وزن کمتر: اسکلت فلزی به دلیل ویژگیهای خاص فولاد، وزن کمتری نسبت به سایر مصالح دارد. به طور میانگین، وزن اسکلتهای فلزی بین 80 تا 190 کیلوگرم برای هر متر مربع است، که نسبت به سایر گزینهها بسیار سبکتر میباشد.
- اشغال فضای کمتر: در ساختمانهایی با ارتفاع و ابعاد مشابه، ستونها و تیرهای فلزی فضای کمتری نسبت به سایر مصالح اشغال میکنند، که این ویژگی به افزایش فضای قابل استفاده در سازههای فلزی کمک میکند.
- پرت کمتر مصالح: مقاطع فولادی که در کارخانهها با استفاده از ماشینآلات مدرن تولید میشوند، دقت بالاتری دارند و این امر موجب کاهش هدررفت مصالح در مقایسه با سایر روشها میشود.
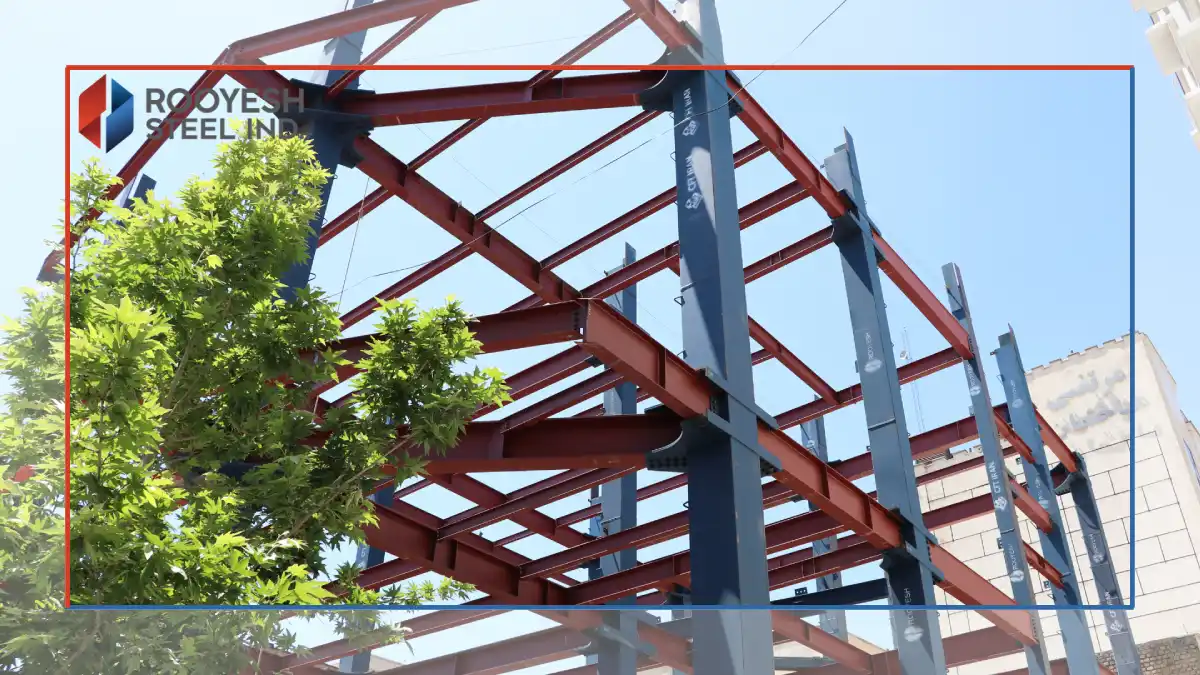
معایب اسکلت فلزی
سازههای فلزی با وجود تمام مزایایی که دارند، واجد معایبی نیز هستند. از جمله مهمترین معایب سازههای فلزی باید به موارد زیر اشاره کرد:
- حساسیت به حرارت: سازههای فلزی شدیدا نسبت به افزایش دما و حرارت حساس هستند. مثلا با افزایش دمای اسکلت تا 600 درجه سانتیگراد، مقاومت کلی سازه به خطر میافتد و ممکن است ساختمان به طور کلی در خطر تخریب قرار بگیرد. این موضوع خصوصا در زمان بروز حوادثی مانند آتشسوزی به طور جدیتری احساس میشود. به نحوی که افزایش ناگهانی حرارت در بخشی از ساختمان میتواند منجر انتقال سریع حرارت به بخشهای دیگر و در نهایت تضعیف مقاومت کل سازه منجر شود. این امر با استفاده از برخی متریال های بر پایه سیمان قابل کنترل می باشد.
- تمایل فطعات فشاری به کمانش: یکی از مهمترین نقاط ضعف و معایب سازههای فلزی، تمایل قطعات به کمانش و در نتیجه آن، تخریب و تضعیف ساختمان است که میتواند خسارات زیادی در پی داشته باشد. لازم به ذکر است که با استفاده از مقاطع و المان هایی که در برابر کمانش مقاومت دارند این امر مرتفع می گردد.
- اشغال فضا: اگر دو ساختمان با ارتفاع و ابعاد یکسان را در نظر بگیریم، ستونها و تیرهای فلزی به مراتب فضای کمتری نسبت به ستونهای بتنی اشغال میکنند و این میتواند منجر به افزایش فضای قابل استفاده در سازههای فلزی شود.
- امکان مقاومسازی و رفع نواقص: در اسکلت فلزی، هر نوع ضعف یا نقص ناشی از محاسبات اشتباه، تغیر قوانین و مقررات یا کمکاری در زمان اجرا را میتواند با جایگزینی آن قطعه برطرف کرد ولی در سازههای بتنی برای رفع برخی نواقص ناگزیر باید نسبت به تخریب بخشهای بزرگی از سازه، حتی بخشهایی بدون نقص اقدام کرد.
- ساخت و نصب سریع و آسان: تهیه مقاطع فولادی در کارخانه و نصب و اتصال آنها در محل پروژه سبب میشود تا به طور کلی روند اجرای اسکلت فلزی سریعتر و آسانتر از سازه بتنی باشد. در واقع و در شرایطی که میتوان عملیات اجرای سازه فلزی را در به طور کامل و یکپارچه پیش برد، برای ساخت سازه بتنی ناگزیر به پیشرفت طبقه به طبقه و مرحله به مرحله هستید.
- ضرورت دقت اجرای پروژه: گرچه اجرای سازه فلزی با پیچ و مهره به طور کلی ایمنتر و مناسبتر است، اما این شیوه بیشتر برای سازههای بزرگ مانند برجها و آسمانخراشها استفاده میشود. در ساختمانهایی که امروزه در ایران ساخته میشوند عمدتا از شیوه جوشکاری برای اتصال قطعات استفاده میشود و به همین دلیل، در برخی موارد در نتیجه مهارت و تجربه کم جوشکار، قدیمیبودن ماشینآلات مورد استفاده یا فقدان نظارت صحیح، مشکلات بزرگی در بخش اتصالات سازه فلزی بروز میکند که میتواند به خسارات جانی و مالی بزرگی بیانجامد.
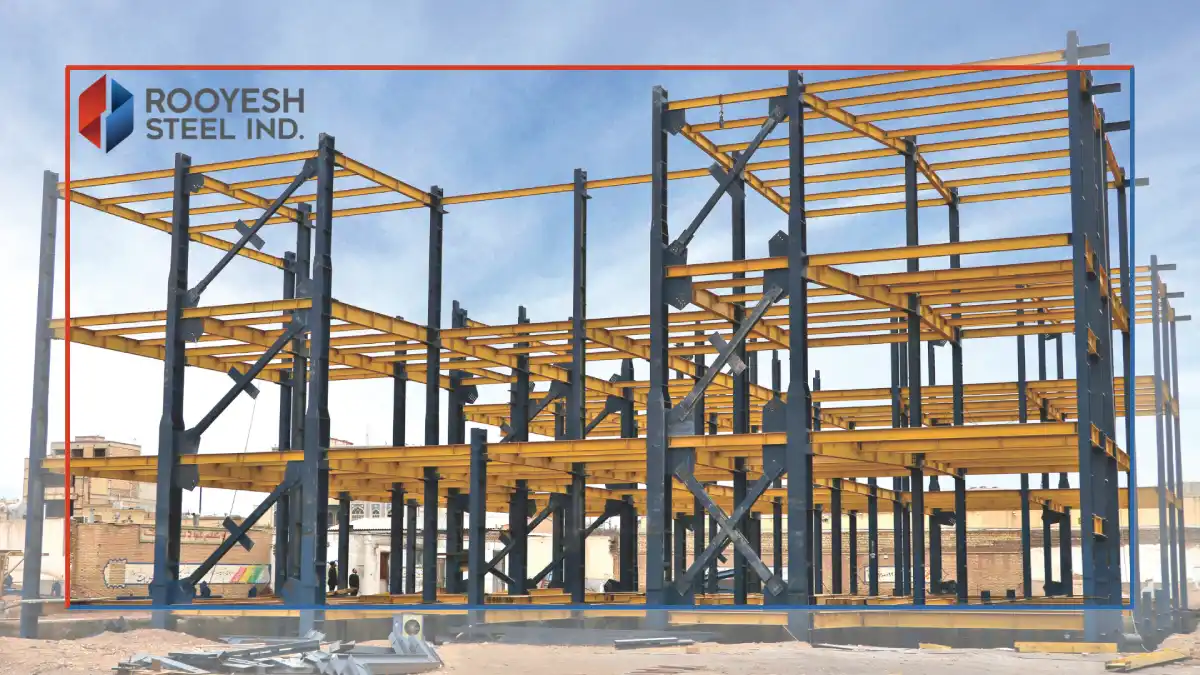
مراحل ساخت ساختمان با اسکلت فلزی
در اینجا لازم به تاکید است که کلیه فرآیند اجرای اسکلت فلزی باید توسط افراد متخصص و باتجربه در این حوزه انجام شود چراکه هر اشتباه کوچکی در این فرآیند میتواند به وقوع خسارات جانی و مالی بزرگی در آینده بینجامد.
مراحل اولیه اجرای اسکلت فولادی
در گام اول اجرای سازه فولادی، لازم است تا محل و زمین اجرای سازه مورد بررسی قرار بگیرد. در این مرحله بهتر است کیفیت و مقاومت خاک مورد آزمایش قرار بگیرد تا از توان آن برای مقاومت در برابر فشار سازه فلزی اطمینان حاصل شود. بعد از این کار، فرآیند خاکبرداری و تسطیح سطح زمین پروژه انجام میشود.
اجرای فونداسیون
در اسکت فلزی یکی از مهمترین بخشهای اجرای آن، اجرای فونداسیون است. اجرای صحیح فونداسیون موجب انتقال صحیح و ایمن نیروهای وارد شده از سازه به خاک می گردد و این امر پایداری سازه روی خاک را تامین می کند.
تمامی نکات طرح و اجرای فونداسیون بر اساس ضوابط آیین نامه های مقررات ملی ساختمان شامل ضخامت فونداسیون، تسطیح خاک، آرماتور بندی و بتن ریزی باید رعایت گردند.
نصب بولتهای صفحه ستون
گام بعدی در اجرای سازه فولادی، نصب بولتهای صفحه ستون است که از اهمیت و حساسیت زیادی برخوردار است. برای تعیین محل نصب بولتها معمولا از دوربینهای نقشهبرداری حرفهای توسط مهندسین استفاده میشود و طبعا باید نحوه اجرای بولتها به شکلی باشد که بعد از بتنریزی نیازی به جابجایی آنها نباشد. معمولا از شابلونهایی مخصوص در این فرآیند استفاده میشود. در صورتی که بولت های جابجایی داشته باشند حتی در حد چند میلیمتر، شابلون مطابق با وضعیت نهایی بولت ها برداشت شده و به کارخانه ساخت اسکلت فلزی منتقل می گردد تا سوراخکاری جای بولت در بیس پلیت مطابق آخرین شرایط موجود انجام شود.
نصب ستونها
ستونها از اهمیت زیادی در هر سازه فولادی برخوردارند چراکه وظیفه مهم انتقال بار و فشارهای وارده به پی یا فونداسیون را دارند و برای این موضوع خود باید از مقاومت بالایی برخوردار باشند.
برپایی ستونها نیز مسئله حساسی است و باید توسط تیمهای حرفهای و با جرثقیلهای قدرتمند انجام شود. مهندسان معمولا برای انواع سازههای فلزی ستونهای مربعی و یا H شکل را توصیه میکنند.
نصب تیرها
بعد از نصب ستونها، فرآیند نصب تیرها بین آنها و اتصالشان به ستونها انجام میشود. معمولا انواع تیرآهن، شاهتیر و تیرچه در این بخش مورد استفاده قرار میگیرد. روش اتصال تیرها به ستون نیز میتواند بسته به نوع سازه یا سفارش کارفرما متفاوت باشد.
راه پله
در صورت لزوم، در گام بعدی باید بر اساس محاسبات انجام شده، فرآیند اجرای راهپله فولادی انجام شود. طرح و اجرای راه پله باید به گونه ای باشد که تیر میان طبقه با معماری تداخل نداشته باشد و اجرای آن موجب سختی کار جرثقیل نشود. لذا زمان اجرا و شیوه اجرای آن اهمیت بالایی دارد.
مهاربند یا بادبند
مهاربند یکی از آخرین مراحل اجرای سازه فولادی است و معمولا بعد از نصب ستونها و تیرها اجرایی میشود. این مهاربندها نقش مهمی در تحمل فشارهای جانبی ناشی از طوفان یا زلزله ایفا میکنند و معمولا با استفاده از نبشی، ناودانی، تسمه و نیمرخ ساخته میشوند.
مصالح مورد استفاده در ساخت اسکلت فولادی
در ساخت اسکلت فلزی از انواع مقاطع فولادی و فلزات با استحکام و آلیاژهای مختلف استفاده میشود. مهمترین اقلام مورد استفاده در اجرای سازه فلزی عبارتند از انواع پروفیل ساختمانی، انواع تیرآهن، انواع ورق فولادی، تسمه فولادی، پیچ و مهره، واشر، میله مهار، الکترود و دیگر موارد لازم.
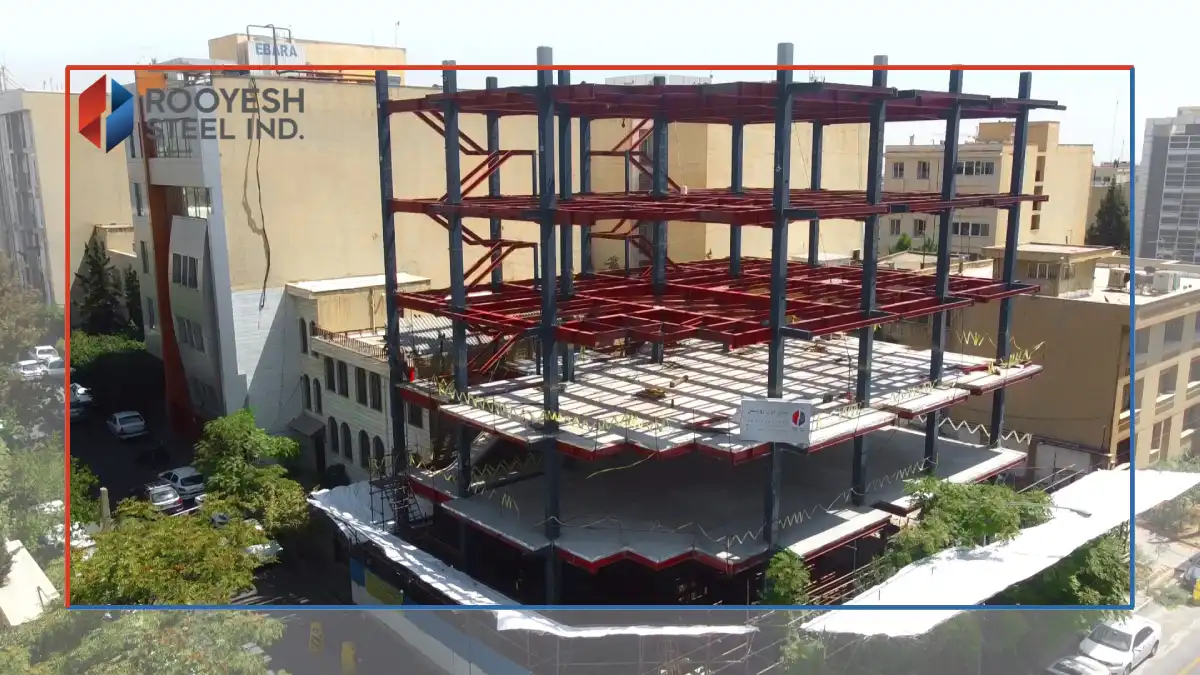
کاربرد اسکلت فلزی چیست؟
در طول مطلب توضیح دادیم که اسکلت فولادی به عنوان یکی از رایجترین شیوههای ساخت اسکلت ساختمان، امروزه در بسیاری از کشورها و برای پروژههای بزرگ و کوچک کاربرد دارد.
اسکلت فلزی از ستونها و تیرهای فلزی تشکیل شده که با پیچ و مهره یا با جوش به هم وصل شدهاند و به دلایلی مانند استحکام بالا، تسریع فرآیند ساخت و ساز، اشغال فضای کمتر و وزن سبکتر نسبت به سازههای بتنی ارجحیت دارد.
امروزه از اسکلت فولادی در ساخت ساختمان، ساخت سوله و کارخانه، پروژههای عمرانی مانند پلها و برجها، پایانههای فرودگاهی و غیره استفاده میشود.
اسکلت فلزی یا بتنی؟
انتخاب بین اسکلت فلزی و بتنی به نیاز پروژه، هزینهها، زمانبندی، شرایط محیطی و عوامل مختلف دیگر بستگی دارد. هرکدام از این دو نوع اسکلت مزایا و معایب خود را دارند:
ویژگی | اسکلت فلزی | اسکلت بتنی |
---|---|---|
وزن | سبکتر | سنگینتر |
سرعت اجرا | سریعتر | زمانبرتر |
مقاومت در برابر زلزله | بهتر (انعطافپذیر) | ضعیفتر (کمتر انعطافپذیر) |
مقاومت در برابر آتش | ضعیفتر (نیاز به پوشش ضد آتش) | مقاومتر |
هزینه | بالاتر | پایینتر |
مقاومت در برابر فشار | ضعیفتر | بسیار مقاوم |
مواد تشکیل دهنده سازه فولادی
فولاد ساختمانی (Structural Steel) به عنوان یکی از انواع فولاد، عمدهترین ماده مورد استفاده در سازههای فولادی گوناگون به شمار میرود. این ماده در گرید ها و اشکال و ابعاد مختلفی شامل تیرآهن، ستون، تیرچه، میلگرد و حتی پیچومهره در سازههای فولادی مورد استفاده قرار میگیرد.
البته لازم به ذکر است که این نوع از فولاد دارای کاربریهای گستردهتری است و به جز سازه فلزی از آن در صنایع معدنی، ترابری، دریایی و صنایع مرتبط با انرژی نیز استفاده میشود.
اساسا، مشخصات مکانیکی فولاد ساختمانی سبب شده تا یکی از گزینههای مناسب و مقاوم برای ساخت انواع ساختمان و پلها باشد. در جدول زیر، ویژگیهای این نوع از فولاد را میبینید:
ویژگی | بازه |
---|---|
چگالی | 7.75 تا 8.1 گرم بر سانتیمتر مکعب |
مدول الاستیسیته | 190 تا 210 گیگاپاسکال |
نسبت پواسون | 0.27 تا 0.3 |
مقاومت کششی | 370 تا 1300 مگاپاسکال |
مقاومت تسلیم | 180 تا 1800 مگاپاسکال |
عدد سختی | 85 تا 630 کیلوگرم |
مراحل تولید سازه فولادی در کارخانه
مراحل تولید سازه فولادی در کارخانه بر اساس نقشه طرح یا سازه که بر اساس جزئیات و اندازهگیری دقیقی تهیه میشود انجام میگیرد. این مراحل عبارتند از؛

طراحی سازه فولادی
امروزه اولین گام در ساخت هر سازهای، طراحی دقیق نقشه آن است. این نقشه در مورد سازههای فلزی اهمیت زیادی دارد چراکه در تمام مراحل اندازهگیری و ساخت مقاطع فلزی در کارخانه و نهایتا برپایی سازه در محل نصب نقشی اساسی دارد. در نتیجه این نقش اساسی بالای نقشه سازه، طراحی آن بایستی ضرورتا توسط مهندسین متخصص انجام شود که به جزئیترین ظرایف سازه فلزی آگاهند.
تامین متریال
در این مرحله و با توجه به جزئیات نقشه سازه فلزی و برآوردهای دقیق انجام شده از قبل، نسبت به سفارش و خرید مقاطع فلزی مورد نیاز در ساخت سازه اقدام میشود. متریال خریداری شده در این بخش در کارخانه و بر اساس نقشه طرح مورد برشکاری، سوراخکاری، جوشکاری و مونتاژ قرار میگیرند.
تمیزکاری و قطعهزنی
این مرحله شامل باز کردن رولها، تمیزکاری ورق، برشکاری، سوراخکاری و پخزنی است. در مواردی ورقها سطوحی چرب یا زنگزده دارند که میتوانند تاثیری مخرب در عملیات جوشکاری ایفا کنند. پس باید قبل از آغاز به کار سطح ورقها از چربی یا هر نوع آلودگی دیگری زدوده شود.
عملیات سند بلاست، اسیدشویی و به کار بردن برسهای سیمی نیز در همین مرحله جهت افزایش کیفیت جوش قطعات انجام میشود.
برشکاری و پخ زنی
برش ورق با استفاده از گیوتین هیدرولیکی و دستگاه Co2 برش، هوابرش، پلاسما و دیگر روشها انجام میشود. برشکاری دیگر مقاطع فلزی مورد استفاده در سازه فولادی مانند میلگرد، نبشی، تیرآهن و غیره نیز در همین مرحله با استفاده از انواع دستگاه برش از جمله اره لنگ و اره آتشی انجام میشود. بعد از برشهای اصلی، به دستگاه برش حرارتی زاویه داده میشود تا پخ لازم جهت انجام جوشهای شیاری داده شود.
تسمه سازی
تسمهسازی صرفا در مورد قطعات ساخته شده از ورق در سازه فولادی کاربرد دارد. از آنجایی که عمده ورقهای برش نخورده در بازار به شکل رولی و در طول 6 متر موجود هستند و انواع دستگاههای برش گیوتین نیز قابلی برش حداکثر 6 متر را دارند، جهت ساخت آن بخش از اجزای سازه فلزی مانند ستونها یا شاهتیرها که طول بیش از 6 متر دارند به تسمهسازی نیاز است.
در این بخش مونتاژ صحیح تسمهها و رعایت دقیق محل قرارگیری بندهای جوش از اهمیت زیادی برخوردار است.
سوراخ کاری
عملیات سوراخکاری مقاطع فلزی مورد استفاده در سازه فولادی بسته به نوع و ضخامت قطعه به دو روش پانچ و دریل انجام میشود. در این مرحله قطعات با توجه به تعداد و نوع سوراخکاری به بخش مورد نظر در کارخانه ارسال و توسط دستگاه مخصوص شابلون، نشانهگذاری و سوراخکاری میشوند.
مونتاژ تیر و ستون
در این مرحله همه قطعاتی که عملیات تسمهسازی و سوراخکاری روی آنها انجام شده مورد مونتاژ اولیه و جوشکاری قرار میگیرند. در این بخش مونتاژ بال و جان تیرها با روش جوشکاری زیر پودری که از روشهای رایج جوشکاری است انجام میشود.
تکمیل کاری
این بخش شامل مونتاژ قطعات الحاقی به سازه فلزی مانند صفحه ستون و پلیتهای تقویتی، قطعات زیرسری و کله گاوی، سختکنندههای داخل ستون و دیگر الحاقات تقویتی هسته ستون است که معمولا به شکل دستی و توسط افراد متخصص انجام میشود.
ساخت قطعات فرعی
همزمان با پیشرفت عملیات ساخت قطعات اصلی سازه بایستی به طور موازی عملیات ساخت و برش دیگر قطعات فرعی مورد استفاده در سازه مانند ورقهای بادبند و مهاربند، دستک طرهها و غیره نیز انجام شود. قطعات این بخش نیز دقیقا مانند روال تهیه قطعات سازه اصلی تمیزکاری، برشکاری، سوراخکاری و مونتاژ میشوند.
تمیزکاری و رنگآمیزی
بعد از تهیه تمام قطعات سازه فولادی، جهت افزایش کیفیت جوش و مونتاژ نهایی سازه، عملیات تمیزکاری و رنگآمیزی مقاطع انجام میگیرد. معمولا دیگر عایقهای حفاظتی نیز در همین مرحله برای قطعات سازه فلزی مورد استفاده قرار میگیرند.
کنترل کیفیت و ارسال به محل نصب سازه فولادی
در پایان مراحل تولید سازه فلزی در کارخانه، عملیات کنترل کیفیت مقاطع سازه فولادی انجام میشود. بعد از اطمینان از کیفیت قطعات مختلف سازه، عملیات پک کردن قطعات، بارگیری و ارسال آنها به محل نصب سازه انجام میشود.
اسکلت فلزی در معماری مدرن؛ ترکیب استحکام و زیبایی در ساختوساز
در دنیای معماری معاصر، اسکلت فلزی بهعنوان یکی از عناصر کلیدی در طراحی و اجرای ساختمانها شناخته میشود. استفاده از فولاد در ساختارهای ساختمانی نهتنها به افزایش مقاومت و دوام سازه کمک میکند، بلکه امکان ایجاد فضاهای باز و طراحیهای خلاقانه را نیز فراهم میسازد. این ویژگیها باعث شدهاند که اسکلت فلزی در پروژههای معماری مدرن، از برجهای بلندمرتبه تا ساختمانهای فرهنگی و تجاری، بهطور گسترده مورد استفاده قرار گیرد.
علاوه بر مزایای فنی، اسکلت فلزی به معماران این امکان را میدهد که با بهرهگیری از فرمها و خطوط ساده و در عین حال زیبا، جلوهای منحصربهفرد به ساختمان ببخشند. ترکیب استحکام ساختاری با زیباییشناسی مدرن، اسکلت فلزی را به انتخابی ایدهآل برای پروژههایی تبدیل کرده است که در آنها عملکرد و ظاهر بهطور همزمان اهمیت دارند. در نتیجه، اسکلت فلزی نهتنها پاسخگوی نیازهای فنی ساختوساز است، بلکه بهعنوان ابزاری قدرتمند در دست معماران برای خلق فضاهای الهامبخش و ماندگار عمل میکند.
در طول این مطلب به کاربرد اسکلت فلزی (سازه فولادی)، نحوه اجرای و مزایا و معایب آن پرداختیم. در شهرهای بزرگ امروزی که محدودیت فضا و مشکلات حملونقل، روند ساختمانسازی را با مشکلات عدیدهای مواجه ساخته، روش سازه فلزی میتواند گزینه بسیار مناسب و مطمئنی برای تسریع روند ساختمانسازی باشد.
الناز
آیا سازه فلزی برای تمام اقلیمها مناسبه؟ مثلاً در مناطقی که رطوبت بالا یا دمای بسیار سرد دارن، چه فکری برای افزایش عمر این سازهها در نظر گرفته میشه؟
اکبری
چرا در برخی پروژههای ساختمانی استفاده از سازه فلزی ترجیح داده میشود و در برخی دیگر سازههای بتنی اولویت دارند؟ آیا استفاده از سازه فلزی همیشه به معنای صرفهجویی در زمان یا هزینه است؟
جلال
درود بر شما
به عنوان کسی که در حوزه ساخت و ساز فعالیت میکنم، اطلاعات ارائه شده در مورد مزایای سازه فلزی، مانند مقاومت بالا، سرعت اجرا و امکان پیشساخته شدن، بسیار مفید بود. به نظر میرسد که سازه فلزی آینده ساختمانسازی است. اما یک سوال مهم این است که با توجه به نوسانات قیمت فولاد، چگونه میتوان هزینههای ساخت سازه فلزی را مدیریت کرد؟ همچنین، آیا میتوان از سازه فلزی در مناطق زلزلهخیز به صورت گستردهتر استفاده کرد؟
ati
سلام، مطالب ارائه شده در مورد انواع اتصالات در سازه فلزی بسیار کاربردی بود. به نظر میرسد که جوشکاری به عنوان متداولترین روش اتصال، از اهمیت ویژهای برخوردار است. اما آیا روشهای جدیدتری مانند اتصالات پیچ و مهرهای یا پرچی نیز میتوانند جایگزین مناسبی برای جوشکاری باشند؟
هاشم کابلی
یکی از مسائلی که ذهنم را مشغول کرده، مقاومت سازه فلزی در برابر زلزله است. آیا این نوع سازهها همیشه بهترین انتخاب برای مناطق زلزلهخیز هستند؟
شاکری
یکی از سوالاتی که همیشه در مورد سازه فلزی برایم مطرح بوده، این است که آیا این نوع سازهها در برابر آتشسوزی هم ایمن هستند؟