برش ورق فولادی یکی از فرآیندهای کلیدی در صنایع مختلف از جمله خودروسازی، ساخت و ساز، کشتیسازی و تجهیزات صنعتی است. این فرآیند شامل استفاده از انواع دستگاههای برش ورق فولادی است که بسته به نوع ورق و نیاز صنعت، روشهای مختلفی برای انجام آن وجود دارد. از جمله این روشها میتوان به برش با لیزر، برش پلاسما، برش مکانیکی و برش با واترجت اشاره کرد. هر یک از این روشها دارای ویژگیهای منحصر به فردی هستند که انتخاب مناسبترین روش به کاربرد خاص و نیازهای تولید بستگی دارد.
فهرست مطالب
برش ورق فولادی
برش ورق فولادی به طور کلی به سه دسته اصلی تقسیم میشود که هر یک برای کاربردهای مشخصی طراحی شدهاند:
برش دقیق (Precision Cutting)
برش دقیق معمولاً برای پروژههایی استفاده میشود که به دقت بالایی نیاز دارند. این روش شامل استفاده از فناوریهای پیشرفتهای مانند برش لیزری یا برش با واترجت است. دقت بالا، امکان تولید قطعات پیچیده و کاهش هدررفت مواد از مزایای این نوع برش است. صنایع خودروسازی و هوافضا از بزرگترین استفادهکنندگان این روش هستند.
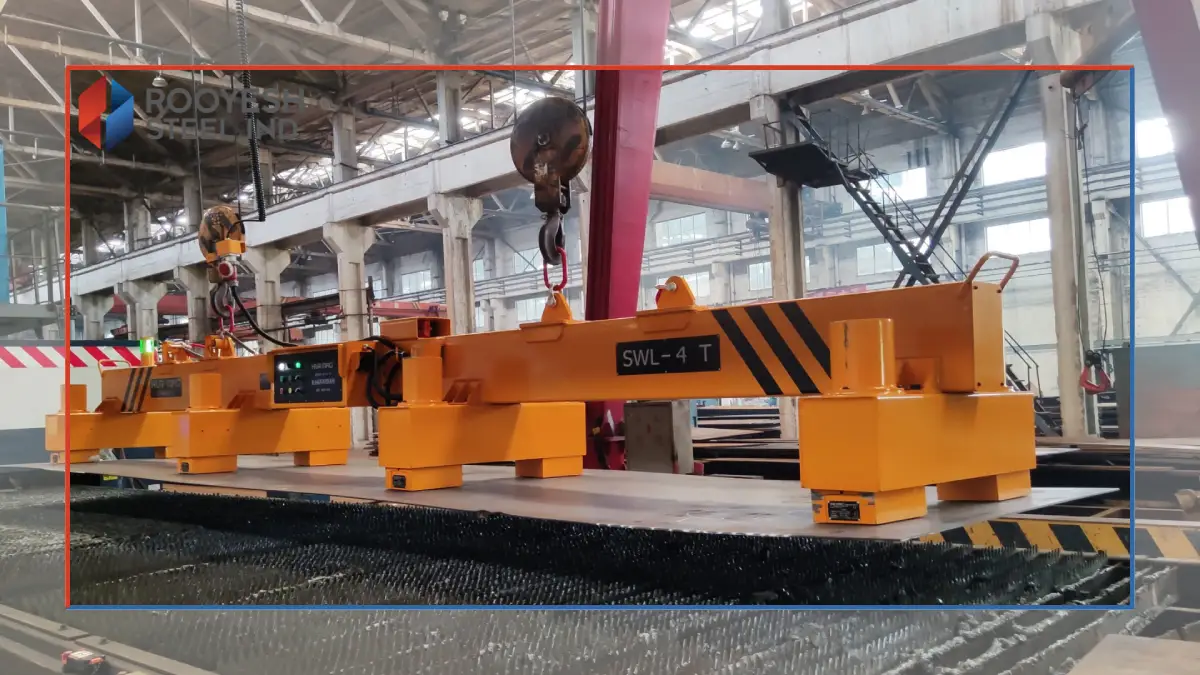
برش سریع (High-Speed Cutting)
این نوع برش برای تولید انبوه و زمانی که سرعت از اهمیت بالایی برخوردار است، به کار میرود. برش پلاسما و برخی از انواع برش مکانیکی در این دسته قرار میگیرند. در این روش، ممکن است دقت کمی کمتر باشد اما سرعت تولید به طور چشمگیری افزایش پیدا میکند.
برش عمومی (General Cutting)
این روشها برای کاربردهای عمومی و زمانی که نیاز به دقت یا سرعت بالا وجود ندارد، استفاده میشوند. برش گیوتین و برخی از انواع برش مکانیکی در این دسته قرار میگیرند. این نوع برش برای پروژههای ساخت و ساز و صنایع سنگین مناسب است.
انواع برش ورق فولادی
برش ورق فولادی به روشهای مختلفی انجام میشود که هر یک ویژگیها، مزایا و معایب خاص خود را دارند. این روشها به چهار دسته اصلی تقسیم میشوند: برش لیزری، برش پلاسما، برش مکانیکی، و برش با واترجت. در ادامه هر یک از این روشها توضیح داده شدهاند:
برش لیزری (Laser Cutting)
برش لیزری یکی از دقیقترین و پیشرفتهترین روشها برای برش ورق فولادی است. در این روش از یک پرتو لیزر متمرکز استفاده میشود که با ایجاد حرارت بالا، ماده را ذوب یا تبخیر میکند و آن را برش میدهد.
- مزایا:
- دقت بالا و توانایی تولید اشکال پیچیده
- کاهش هدررفت مواد
- مناسب برای ورقهای نازک و ضخامتهای متوسط
- سرعت بالا برای برش طرحهای پیچیده
- معایب:
- هزینه بالای تجهیزات
- محدودیت در برش ورقهای با ضخامت بسیار بالا
- نیاز به اپراتور ماهر و محیط کار کنترلشده
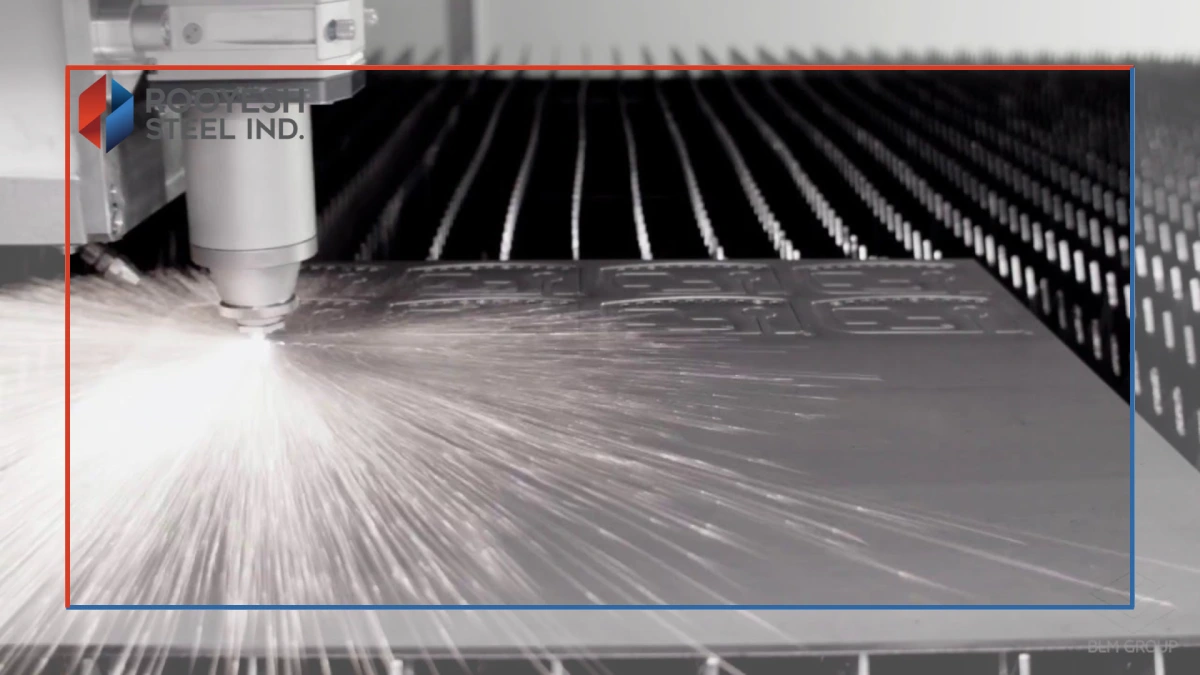
برش پلاسما (Plasma Cutting)
این روش از یک جت پلاسما با دمای بسیار بالا (هزاران درجه سانتیگراد) برای ذوب کردن و جدا کردن فلز استفاده میکند. برش پلاسما بیشتر برای برش ورقهای ضخیم و زمانی که سرعت اهمیت دارد، کاربرد دارد.
- مزایا:
- سرعت بالا در برش
- توانایی برش ورقهای ضخیم
- هزینه نسبتاً کمتر نسبت به برش لیزری
- معایب:
- دقت کمتر نسبت به برش لیزری
- ایجاد حرارت زیاد که ممکن است باعث تغییر ساختاری در ماده شود
- تولید لبههای برش که نیاز به اصلاح دارند
برش مکانیکی (Mechanical Cutting)
این روش شامل استفاده از دستگاههایی مانند گیوتین، اره دیسکی یا پانچ است که نیروی مکانیکی را برای بریدن ورق اعمال میکنند.
- مزایا:
- هزینه پایین تجهیزات و بهرهبرداری
- سادگی فرآیند و عدم نیاز به تجهیزات پیچیده
- مناسب برای برش ورقهای ضخیم و کاربردهای عمومی
- معایب:
- دقت کمتر نسبت به روشهای لیزری و واترجت
- لبههای ناهموار که ممکن است نیاز به پولیش داشته باشند
- محدودیت در ایجاد اشکال پیچیده
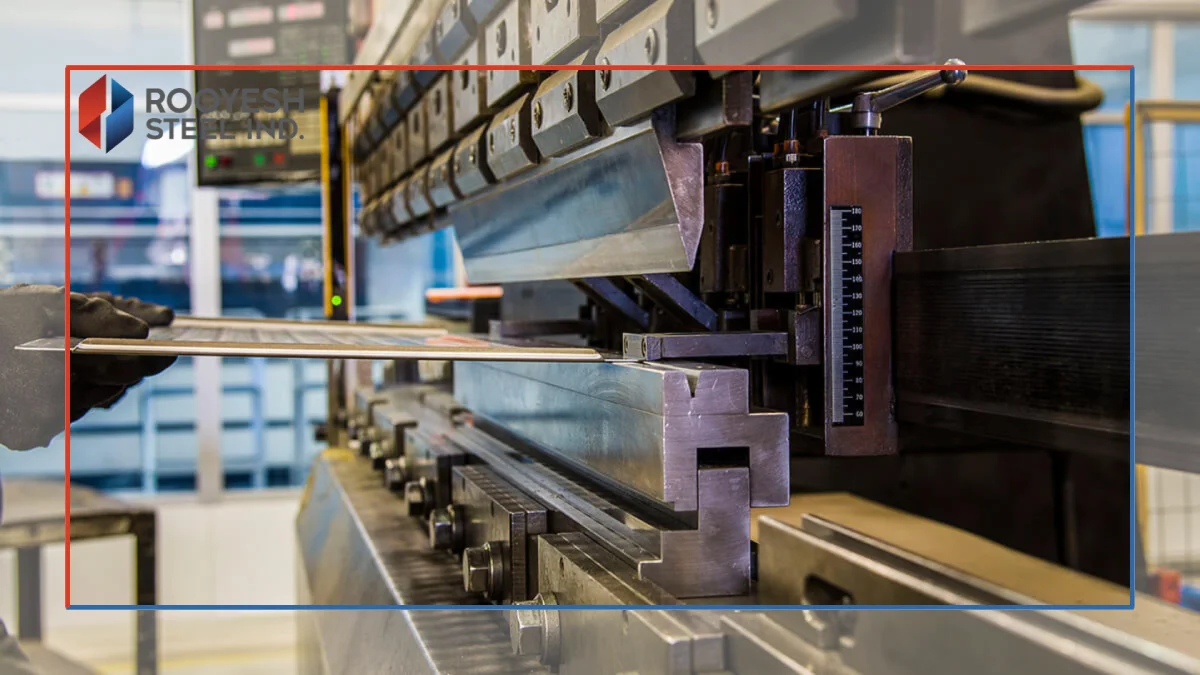
برش با واترجت (Waterjet Cutting)
در این روش، یک جت آب با فشار بسیار بالا (گاهی همراه با مواد ساینده) برای بریدن ماده استفاده میشود. این روش برای موادی که نمیتوانند حرارت زیاد را تحمل کنند، ایدهآل است.
- مزایا:
- بدون ایجاد حرارت و تغییر ساختاری در ماده
- امکان برش انواع مواد مختلف (فلزات، شیشه، پلاستیک و غیره)
- دقت بالا در برش
- معایب:
- هزینه بالای تجهیزات و نگهداری
- سرعت کمتر نسبت به برش پلاسما و مکانیکی
- محدودیت در برش ورقهای بسیار ضخیم
روش | دقت | هزینه | سرعت | ضخامت قابل برش |
---|---|---|---|---|
برش لیزری | بسیار بالا | بالا | متوسط | متوسط |
برش پلاسما | متوسط | متوسط | بسیار بالا | بالا |
برش مکانیکی | پایین | پایین | بالا | متوسط تا بالا |
برش واترجت | بسیار بالا | بالا | متوسط | بالا |
هر روش بسته به نیاز پروژه، نوع ماده و بودجه، میتواند انتخابی بهینه باشد. انتخاب مناسبترین روش به دستیابی به کیفیت بهتر، صرفهجویی در هزینه و افزایش بهرهوری کمک میکند.
مراحل انجام انواع برش ورق فولادی
- بررسی نیاز پروژه: ابتدا نیازهای پروژه از جمله دقت مورد نیاز، ضخامت ورق و نوع ماده مشخص میشود.
- انتخاب روش مناسب برش: براساس نیازهای تعیینشده، یکی از روشهای برش لیزری، پلاسما، مکانیکی یا واترجت انتخاب میشود.
- آمادهسازی ورق فولادی: ورق باید تمیز شده و در صورت نیاز بر روی میز برش قرار گیرد.
- اجرای فرآیند برش: با استفاده از دستگاه مربوطه، فرآیند برش آغاز میشود. در این مرحله کنترل کیفیت برش بسیار مهم است.
- اصلاح لبهها (در صورت نیاز): در برخی موارد، لبههای برشخورده ممکن است نیاز به اصلاح یا پولیش داشته باشند.
مزایا و معایب انواع برش ورق فولادی
مزایا:
- دقت بالا (در روشهای لیزری و واترجت)
- سرعت تولید بالا (در روشهای پلاسما و مکانیکی)
- تنوع در برش مواد مختلف
- امکان تولید اشکال پیچیده با برش لیزری
- کاهش هدررفت مواد (به ویژه در روشهای دقیق)
معایب:
- هزینه بالای تجهیزات در روشهای پیشرفته مانند لیزر و واترجت
- نیاز به اپراتور ماهر
- محدودیت در ضخامت ورق برای برخی روشها
- نیاز به تعمیر و نگهداری مداوم دستگاهها
انواع دستگاههای برش ورق فولادی
دستگاههای مختلفی برای برش ورق فولادی در بازار وجود دارند که هر یک برای کاربرد خاصی مناسباند:
- دستگاه برش لیزری: برای کاربردهای دقیق و پیچیده.
- دستگاه برش پلاسما: مناسب برای برش سریع و ورقهای ضخیم.
- گیوتین: دستگاهی ساده و کارآمد برای برشهای عمومی.
- اره دیسکی: برای برش مکانیکی و کاربردهای ساده.
- دستگاه واترجت: برای برشهای بدون تغییر حرارتی.
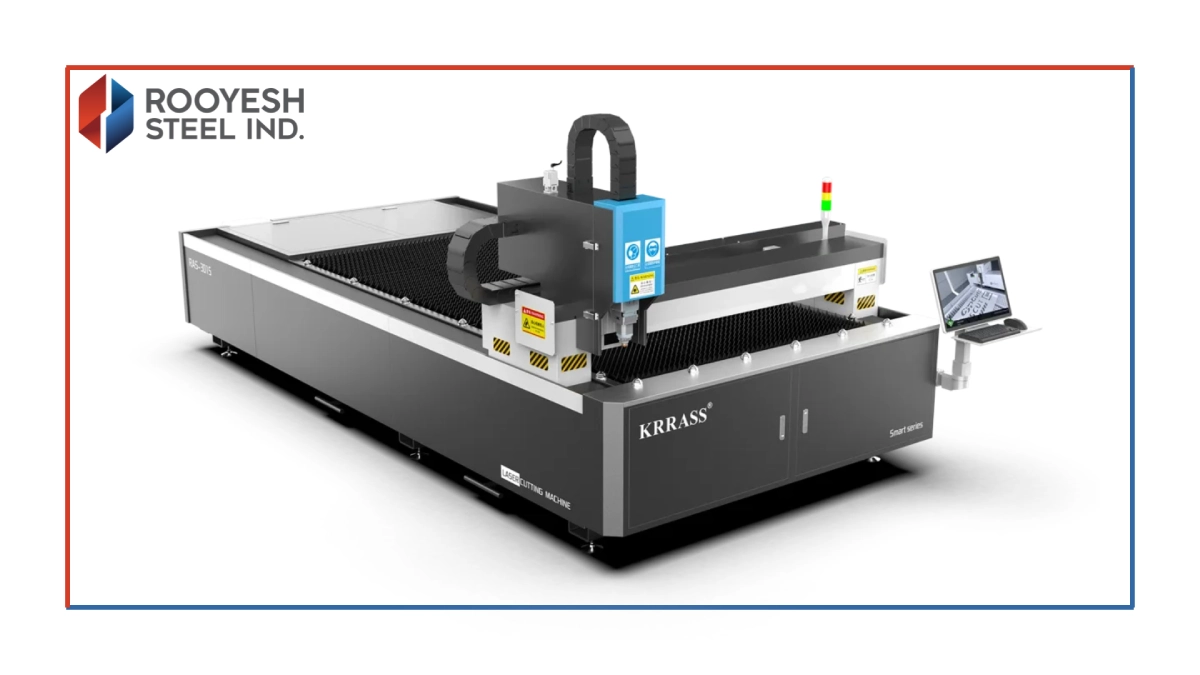
برش ورق فولادی یکی از فرآیندهای اساسی در تولیدات صنعتی است که با استفاده از انواع دستگاههای برش ورق فولادی انجام میشود. انتخاب روش و دستگاه مناسب تأثیر مستقیمی بر کیفیت و کارایی فرآیند دارد. با توجه به تنوع روشها و فناوریهای موجود، نیاز است تا بر اساس نوع پروژه و ویژگیهای ماده، بهترین گزینه انتخاب شود تا هزینهها کاهش یابد و بهرهوری افزایش پیدا کند.