تفاوت بریکت و آهن اسفنجی چیست؟ بریکت و آهن اسفنجی، دو روی یک سکه یا دو مسیر متفاوت در صنعت فولاد؟ در نگاه اول، شاید این دو ماده تفاوت چندانی نداشته باشند، اما اگر عمیق تر به ماهیت آن ها دقت نظر داشته باشیم، متوجه خواهیم شد که هرکدام ویژگی های متمایزی دارند که قطع به یقین تأثیر بسزایی در فرآیندهای فولادسازی می گذارند. در ادامه به شما خواهیم گفت که آیا بریکت همان آهن اسفنجی فشرده شده است؟ یا اینکه تفاوت های ساختاری و کاربردی، این دو را از هم جدا می کند؟ این دو ماده ارزشمند در صنعت فولاد را به طور کاملا تخصص و موشکافانه بررسی نموده و پرده از راز تفاوت های آنها بر میداریم. پس با ما همراه باشید.
فهرست مطالب
بریکت چیست؟
رمز فشرده سازی در صنعت فولاد با بریکت، تحقق پیدا می کند. اجازه بدهید کمی ساده تر صحبت کنیم. بریکت (Briquette) نوعی ماده فشرده شده است که از ذرات ریز مواد اولیه فلزی مانند آهن اسفنجی، نرمه سنگ آهن، گرد و غبار فولاد سازی یا ضایعات فلزی تولید می شود. این فرآیند به منظور کاهش هدر رفت مواد، افزایش چگالی و بهبود حمل و نقل و ذخیره سازی انجام می گیرد. لازم به ذکر است که فرآیند فشرده سازی به دلایل متعددی قابل انجام است که مهم ترین آن ها افزایش چگالی، ذخیره سازی آسان تر و کاهش اکسیداسیون و آلودگی محیطی است.
به بیان ساده تر اینکه، در فرآیندهای تولید فولاد، مقادیر زیادی از مواد اولیه به شکل پودر یا ذرات ریز تولید می شود که در صورت عدم استفاده، هدررفت منابع ارزشمند و ایجاد مشکلات زیست محیطی را به دنبال دارد. بریکت سازی این مواد را به شکل جامد و متراکم در میآورد و آن ها را به یک منبع قابل استفاده در کوره های ذوب فولاد مبدل خواهد ساخت.
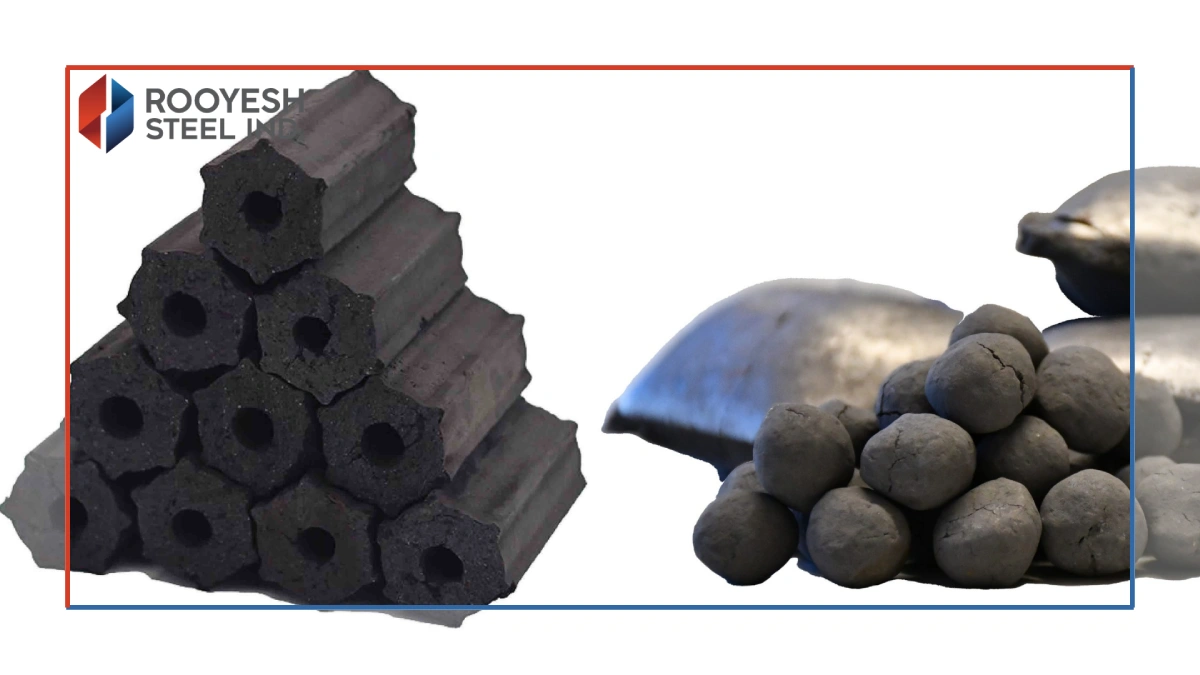
ویژگی های بریکت
در بحث پرداختن به تفاوت بریکت و آهن اسفنجی لازم است که با ویژگی این محصولات آشنا شویم. در واقع، بریکت از مهم ترین مواد اولیه در فولاد سازی به شمار رفته و دارای ویژگی های منحصر به فردی است.
- چگالی بالاتر نسبت به آهن اسفنجی به جهت فرآیند فشرده سازی
- مقاومت مکانیکی بیشتر که از خرد شدن و هدر رفت مواد جلوگیری میکند
- کاهش فضای موردنیاز برای ذخیره سازی و بهینه سازی حمل و نقل
- مقاومت بیشتر در برابر اکسیداسیون نسبت به آهن اسفنجی
- کاهش احتمال زنگ زدگی و افت کیفیت در اثر رطوبت و هوا
- امکان ذخیره سازی در محیط های باز بدون نگرانی از احتراق خود به خودی
- ریسک پایین تر در جا به جایی های طولانی مدت و صادراتی
- کاهش ضایعات و گرد و غبار در حین جا به جایی
- جایگزین مناسبی برای آهن اسفنجی و قراضه آهن در کوره های قوس الکتریکی و القای
- افزایش بهرهوری فرآیند ذوب به خاطر چگالی بالاتر و ترکیب یکنواخت
- کاهش مصرف انرژی و زمان ذوب به علت ساختار متراکم تر
انواع مختلف بریکت برای کاربردهای متنوع
وقتی، بهتر تفاوت بریکت و آهن اسفنجی را درمک می کنید که بدانید بریکت در سه نوع اصلی تولید می شود.
- بریکت گرم آهن اسفنجی (HBI): بیشترین استحکام و چگالی، مناسب برای صادرات و حمل و نقل های طولانی مدت
- بریکت سرد آهن اسفنجی (CBI): چگالی کمتر از HBI ولی همچنان مقاوم در برابر اکسیداسیون
- بریکت نرمه آهن اسفنجی: بازیافت و استفاده مجدد از گرد و غبار آهن اسفنجی در فرآیند فولادسازی
آهن اسفنجی چیست؟
آهن اسفنجی، شاهکلید تولید فولاد با خلوص بالا، از احیای مستقیم سنگ آهن به دست میآید. در این فرآیند، بدون ذوب شدن سنگ آهن، اکسیژن آن حذف می شود و آهنی با درصد خلوص بالا تولید میگردد. شکل ظاهری این ماده شبیه به تکه های اسفنجی متخلخل است، از این رو به آن آهن اسفنجی می گویند. فرآیند تولید آهن اسفنجی به شرح زیر است:
- به منظور تولید آهن اسفنجی از فرآیند احیای مستقیم (DRI – Direct Reduced Iron) استفاده می شود. در این روش:
- سنگ آهن به شکل گندله یا کلوخه در کوره های احیای مستقیم قرار می گیرد.
- گازهای احیاکننده مانند گاز طبیعی (متان) یا زغال سنگ، اکسیژن موجود در سنگ آهن را حذف می کنند.
- محصول نهایی آهن اسفنجی با خلوص بالا است که برای تولید فولاد استفاده می گردد.
تفاوت بریکت و آهن اسفنجی
در راستای پرداخات به موضوع تفاوت بریکت و آهن اسفنجی باید به این موضوع اشاره داشته باشیم که هر دو برای قراضه آهن استفاده می شوند. با این حال، شاهد تفاوت های ساختاری، فرآیند تولید، خواص فیزیکی و کاربردهای متفاوت آنها هستیم.
ماهیت و ساختار فیزیکی
آهن اسفنجی بهعنوان محصول فرآیند احیای مستقیم سنگآهن تولید میشود و به دلیل تخلخل بالا، ظاهری اسفنجی دارد. این ماده به شکل قطعات کوچک و متخلخل است که قابلیت جذب سریع اکسیژن را دارد و همین موضوع باعث میشود در مجاورت هوا بهسرعت اکسید شود.
بریکت یک ماده فشردهشده است که از ترکیب نرمه آهن اسفنجی یا سایر مواد فلزی در فرآیند بریکتسازی به دست میآید. این ماده در قالبهای متراکم تولید میشود و نسبت به آهن اسفنجی، چگالی بالاتر، مقاومت مکانیکی بیشتر و پایداری بهتری در برابر اکسیداسیون دارد.
فرآیند تولید
آهن اسفنجی از طریق فرآیند احیای مستقیم سنگآهن با استفاده از گازهای احیاکننده (مانند گاز طبیعی) یا زغالسنگ تولید میشود. در این روش، اکسیژن سنگآهن بدون نیاز به ذوب حذف شده و آهن با درصد خلوص بالا حاصل میگردد.
بریکت از طریق فشردهسازی و متراکمسازی آهن اسفنجی یا نرمه آن تولید میشود. فرآیند بریکتسازی با استفاده از دستگاههای پرس تحت دمای بالا (برای بریکت گرم) یا در شرایط سرد (برای بریکت سرد) انجام میشود. در نتیجه، ذرات ریز آهن اسفنجی به یک ماده مستحکم و پایدار تبدیل میشوند که حملونقل و ذخیرهسازی آن آسانتر از آهن اسفنجی است.
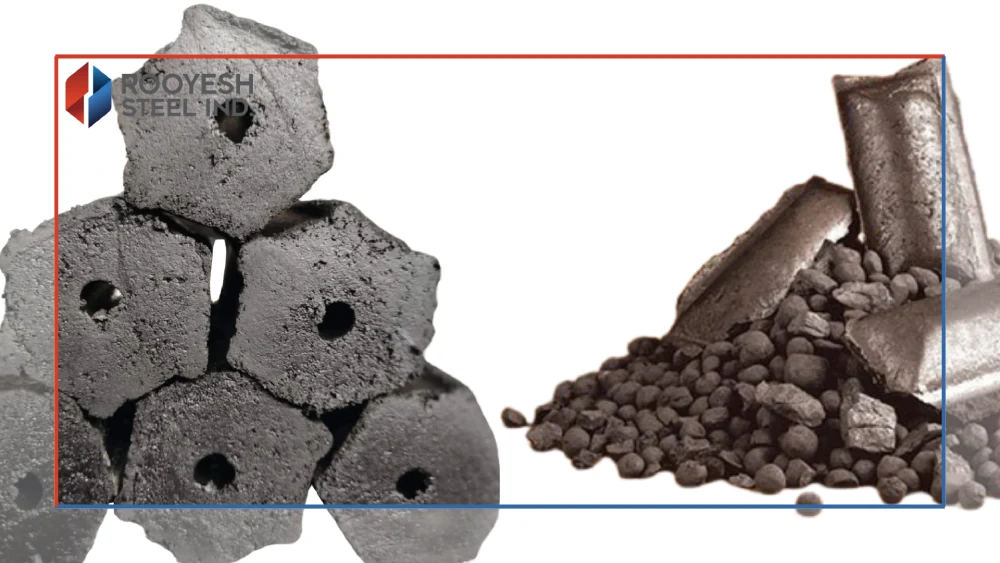
انواع و دستهبندی
آهن اسفنجی معمولاً بهصورت یک محصول خام و متخلخل ارائه میشود که برای استفاده در کورههای ذوب به کار میرود. این ماده مستقیماً به کورههای قوس الکتریکی یا القایی تغذیه شده و به فولاد مذاب تبدیل میشود.
بریکت بسته به روش تولید و شرایط فشردهسازی، به سه نوع اصلی تقسیم میشود:
- بریکت گرم آهن اسفنجی (HBI): در دمای بالا و تحت فشار زیاد تولید شده و دارای چگالی بالا، استحکام بیشتر و مقاومت عالی در برابر اکسیداسیون است.
- بریکت سرد آهن اسفنجی (CBI): در دمای محیط فشرده شده و تراکم آن کمتر از HBI است، اما همچنان قابلیت استفاده در کورههای ذوب را دارد.
- بریکت نرمه آهن اسفنجی: از گرد و غبار و نرمههای آهن اسفنجی که در فرآیند تولید به هدر میروند، ساخته شده و در فولادسازی استفاده میشود.
حملونقل و ذخیرهسازی
آهن اسفنجی به دلیل تخلخل زیاد و سطح فعال بالا، بهشدت مستعد اکسید شدن در مجاورت هوا است. این خاصیت باعث میشود حملونقل و ذخیرهسازی آن با چالشهایی همراه باشد، زیرا در تماس با رطوبت یا اکسیژن، امکان خودسوزی و زنگزدگی آن وجود دارد.
در مقابل، بریکت (مخصوصاً HBI) به دلیل چگالی بالا و سطح فشردهشده، در برابر اکسیداسیون مقاومتر است و در نتیجه، حملونقل و ذخیرهسازی آن ایمنتر و کمریسکتر از آهن اسفنجی است. این ویژگی باعث میشود که بریکت بهعنوان گزینهای ایدهآل برای صادرات و جابهجایی در مسافتهای طولانی مورد استفاده قرار گیرد.
کاربرد در فولادسازی
آهن اسفنجی مستقیماً در کورههای قوس الکتریکی و القایی برای تولید فولاد مورد استفاده قرار میگیرد. این ماده بهعنوان جایگزین قراضه آهن، باعث کاهش ناخالصیها و افزایش کیفیت فولاد تولیدی میشود.
بریکت نیز همانند آهن اسفنجی، در فرآیندهای فولادسازی استفاده میشود، اما به دلیل ویژگیهای مکانیکی بهتر، در برخی موارد جایگزین بهتری نسبت به آهن اسفنجی محسوب میشود. مخصوصاً بریکت گرم (HBI) به دلیل مقاومت بالا در برابر اکسیداسیون و سهولت در حملونقل، انتخابی ایدهآل برای کارخانههایی است که مواد اولیه خود را از نقاط دور تأمین میکنند.
مزایا و معایب
مزایای آهن اسفنجی:
- درصد خلوص بالا و جایگزینی مناسب برای قراضه
- کاهش ناخالصیها در فرآیند تولید فولاد
- قابلیت استفاده مستقیم در کورههای قوس الکتریکی و القایی
معایب آهن اسفنجی:
- حساسیت بالا به اکسیداسیون و خودسوزی
- حملونقل و ذخیرهسازی دشوار
- چگالی پایین و حجم بیشتر نسبت به بریکت
مزایای بریکت:
- چگالی بالا و حملونقل آسانتر
- مقاومت بیشتر در برابر اکسیداسیون و زنگزدگی
- کاهش هدررفت مواد و بهبود بهرهوری
معایب بریکت:
- فرآیند تولید پیچیدهتر نسبت به آهن اسفنجی
- هزینه بریکتسازی ممکن است بالاتر باشد
انتخاب بین آهن اسفنجی و بریکت بستگی به شرایط حملونقل، نیازهای فولادسازان و نوع فرآیند تولید فولاد دارد. اگر کارخانهای به مواد اولیه با خلوص بالا و بدون هزینه اضافی فرآوری نیاز داشته باشد، آهن اسفنجی گزینه مناسبی است. اما اگر پایداری در ذخیرهسازی، ایمنی در حملونقل و کاهش اکسیداسیون اهمیت داشته باشد، بریکت (مخصوصاً HBI) انتخاب بهتری خواهد بود.
- اگر مصرف داخلی و کوتاهمدت مدنظر باشد، آهن اسفنجی انتخاب خوبی است.
- اگر حملونقل طولانیمدت و ذخیرهسازی بدون ریسک مهم باشد، بریکت (خصوصاً HBI) ارجحیت دارد.
پس، بریکت و آهن اسفنجی دو روی یک سکه در صنعت فولاد هستند! اما بسته به شرایط، انتخاب مناسب میتواند هزینهها را کاهش داده و بازدهی تولید را افزایش دهد.